Shanghai IVEN Pharmatech Engineering Co., Ltd was established in 2005, with great efforts we developed four excellent plants for pharmaceutical machinery, blood collection tube machinery, water treatment equipment and clean room facilities. We’re the pioneer supplier in China to provide integrated engineering solution for worldwide pharmaceutical factory and medical factory in compliance with EU GMP / US FDA standard and WHO principle. Our company cooperates closely with well-known scientific research institutions and pharmaceuticals industry designing institutes to provide the most reasonable project design, the best quality equipment and the customized service to different pharmaceutical / medical factories from different markets. IVEN’s integrated engineering solutions for pharmaceutical and medical factory include the clean room, auto-control and monitoring system, pharmaceutical water treatment system, solution preparing and conveying system, filling and packing system, automatic logistics system, quality control system, central laboratory and etc. Focused on customers’ individual requirements, IVEN customizes engineering solutions meticulously for users on: *Pre-engineering consulting service *Production process selection *Equipment model selection and customization *Installation and commissioning *Validation of the equipment and process *Production technology transferring *Hard and soft documentation *Training for skilled workers and so on. Based on the needs of users from worldwide, IVEN continuously doing a lot of deep research and study on the development of pharmaceutical and medical industry, pursue the endless improvement of our machinery and project quality. We will sincerely cooperate with pharmaceutical and medical enterprises from worldwide and make unremitting efforts for human health.99999
-
Integrated Blood Collection Tube Production Line (after labeling)
Brief introduction & Advantage Tail-labeling machine connected online, non-label tube to be auto detected by world leading image technology after stoppering & capping and vacuuming (including rift of stopper or cap or glass tube, foreign matter inside tube, no additive, less additi
0 -
Handmade paper honeycomb laminboards
Handmade paper honeycomb laminboards, high-quality color coated steel for the surface layer, the inner clip retardant paper honeycomb core material, using handmade crafts. Surrounded adopts iron or aluminum keel keel box. This product is convenient and quick construction of the installation, overall
- Contacter: Charlene Liu
- Tel: +86-21-58716151
- Fax: +86-21-50760379
- Email: iven@pharmatechcn.com
-
Company Address:
NO.201, New Jinqiao Rd, Pudong, Shanghai, China
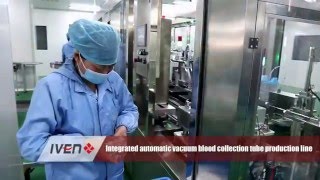
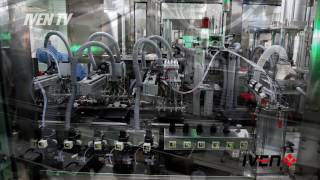

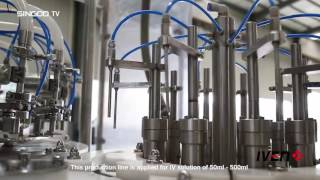
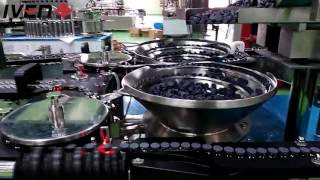
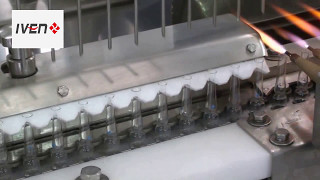
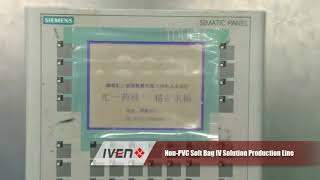