Our Video
Shanghai Longda Alloy Material is a Wholly Owned Subsidiary company of Wuxi Longda Metal, offers Copper alloys, High Performance alloys and Nickel-based, Cobalt based high temperature alloys for the global market. These alloys are highly engineered to offer a superior combination of heat resistance, high-temperature corrosion resistance, toughness and strength properties.
Share
Hot Products
-
Nickel Based Vacuum Melted Superalloys
Longda Super alloy company’s Nickel based super alloy bars, such as Inconel 713, Inconel 738LC, Inconel 718, Inconel 792, Inconel 939,Inconel 625, GTD 111,GTD 222 etc are very high purity, consistent quality and homogenized that satisfied to our customers home and abroad. Nickel based super alloys
Contact Us
- Contacter: info@wxlongda.com
- Tel: 0086-510-88786098
- Fax: 0086-510-88722222
- Email: info@wxlongda.com
-
Company Address:
Room 310-09, Floor 3, Building No.2, No.38,Debao Rd,China (Shanghai) Pilot Free Trade Zone
Products
Copper Mould Tube
Copper moulds for billet and slab continuous casting machines
Shanghai Longda Alloy offers a wide range of associated equipment necessary for steady operation of steel production plants. Especially, in order to increase the efficiency of the continuous casting machines (CC machines) along with reducing of involved maintenance efforts,Longda has to offer a wide program of caster moulds already proven at metal production plants in China and conform to the customer’s requirements in their quality and price.
One of the continuous casting machine components relevant for high quality of semi-finished metal casting products is a mould. The CC machine mould includes the mould tube / plate that contacts directly with liquid metal, steel body fixing the mould and cooling jacket for effective cooling of molten metal.
Copper mold tube / plate is the most critical and high wearing part of the mould. In contact with liquid metal the copper mould forms an ingot by cooling a thin shell of metal and forming a solid crust. By extracting of the still-solidifying ingot and continuous feeding of molten metal to the mould a continuous strand is formed, that format is determined by the mould shape.
Copper moulds for billet and slab continuous casting machines.We can provide copper moulds include:
Square Crystallizer Copper tube
Rectangle Crystallizer Copper tube
Round Crystallizer Copper tube
Special Shapes Crystallizer Copper tube
Beam Blank Crystallizer Copper tube
Flanging Crystallizer Copper tube
Slab Mould plates
The mould quality, especially its wear resistance and service life of contacting surfaces, determines the efficiency and shutdown times of continuous casting machine. The mould service life can be of 3,000 to 4,000 tons of steel.
The billet and slab casting moulds can vary as follows:
Length (from 500 mm to 1200 mm):
Straight
Parabolic
Two, three and four – cone shaped straight
Multi-cone shaped parabolic
Cross section:
Round (Dia.from 110 mm-1500mm)
Rectangular or square (up to 650 mm)
Mould plates for slab casting machines
The Shanghai Longda Alloy can also supply special copper mould tubes/plates of special length and geometry based on individual drawings made in accordance with provided customer’s specifications.
According to physical and chemical characteristics of casted metal the mould tubes for casting machines can differ in materials that are used in their construction:
Refined copper (99,90 % and more pure),
CuAg alloy,
CuCrZr alloy,
Beryllium Copper
In order to increase the erosion resistance and service life the casting machine mould tubes are special coated. The mould tubes can be provided with different types of internal surface coating:
One-layer chromium coating. Thickness from 0,12 to 0,22 mm, hardness 900 HV.
One-layer nickel coating. Hardness up to 1200 HV (for different steel grades with high crack susceptibility)
Three-layer nickel-cobalt-chromium coating.
Main Production processes:
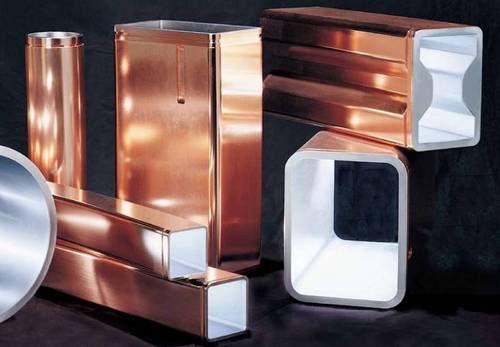