Farfly Company was established in 2003 with 1000 million fund registered. The headquarters located at Hongqiao International square of the big Hongqiao’s business district. Two manufacturing base respectively located at Fenxian chemical industrial park of Shanghai and Gushan industrial park of wuxi city, Jiangsu province. China Farfly is a specialized manufacturer in Chemical machinery equipment with total area about 18,000 square meters.
-
FCT10000 Coating complete quipment
●With annual capacity of 5000~10000T, it can meet production demands of large-scale coating manufactorers. ●Well preassembling of batch charging, milling, paint mixing, filling, control system, at the time of ex-factory and with field’s assembly of assistance program, it can form pr
-
Dispering reactor&Tinting reactor
●Applicable for concocting finished products or mixing different phases of materials in coating, dyes, pigments, printing inks, pesticide and paper-making industries, etc. It can be fitted with many kinds of mixers, which are suitable for different working conditions. ●As per different
93
- Contacter: 王嫣
- Tel: 021-51093066
- Fax: 021-36377608
- Email: export@farfly.com
-
Company Address:
NO.501.Yuzhuang Rd.,Fengxian District,Shanghai China
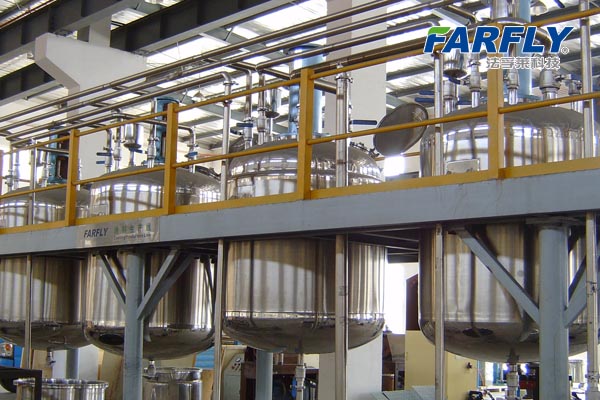
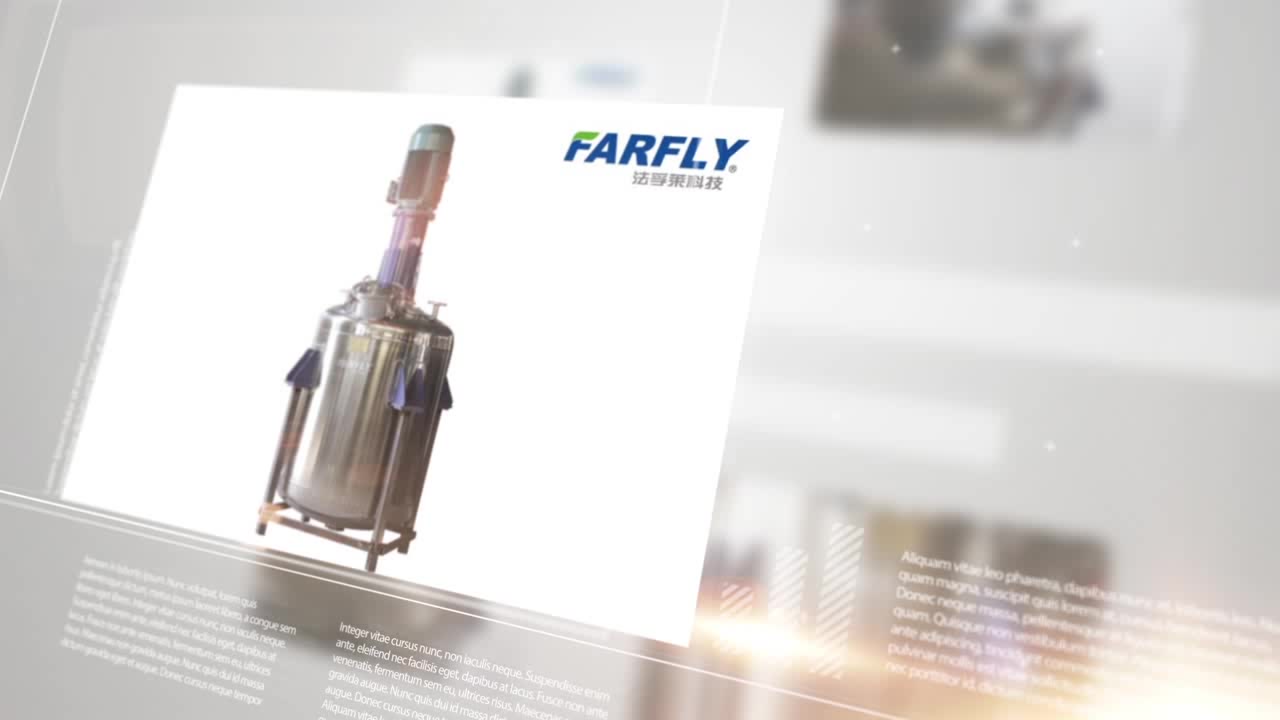
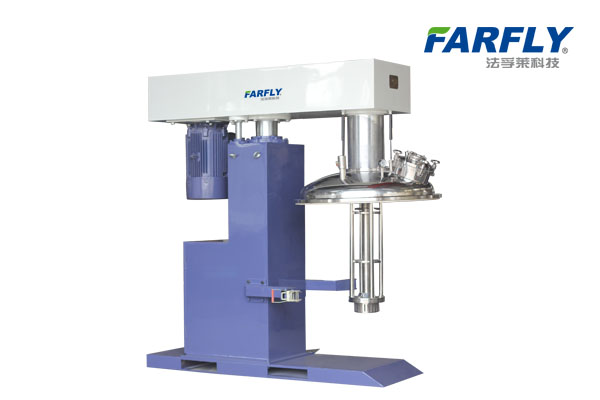
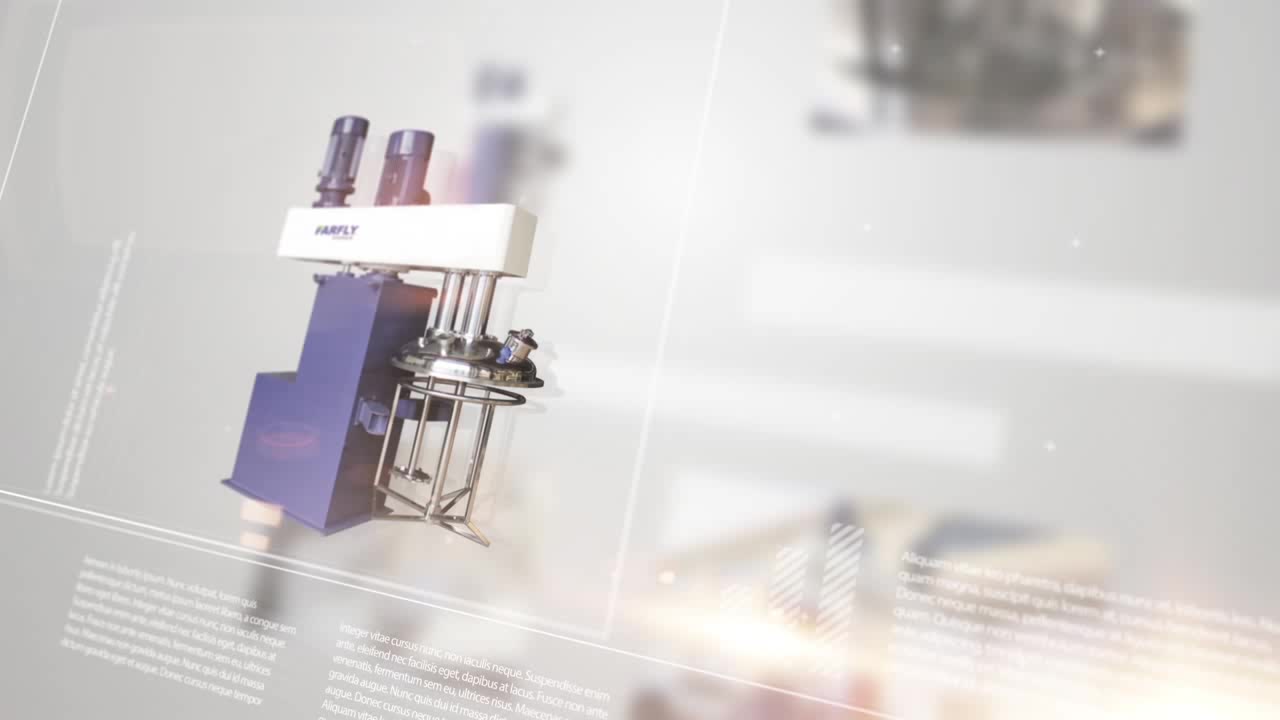
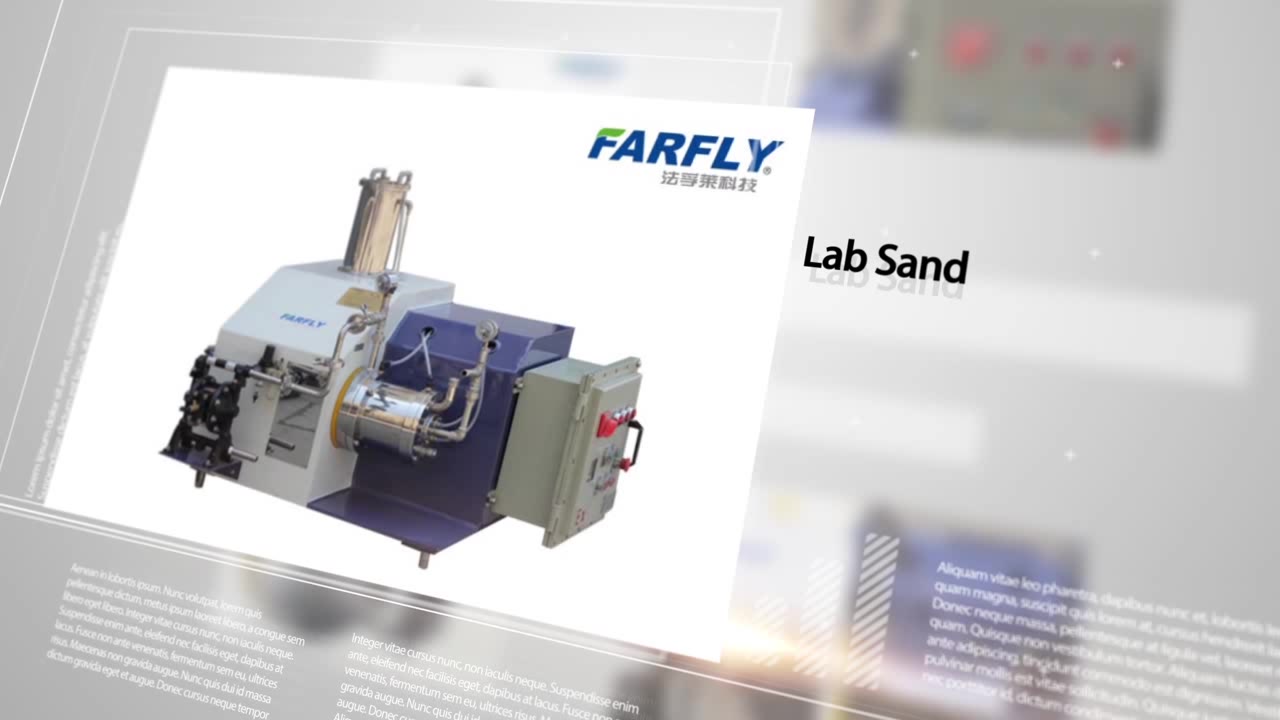
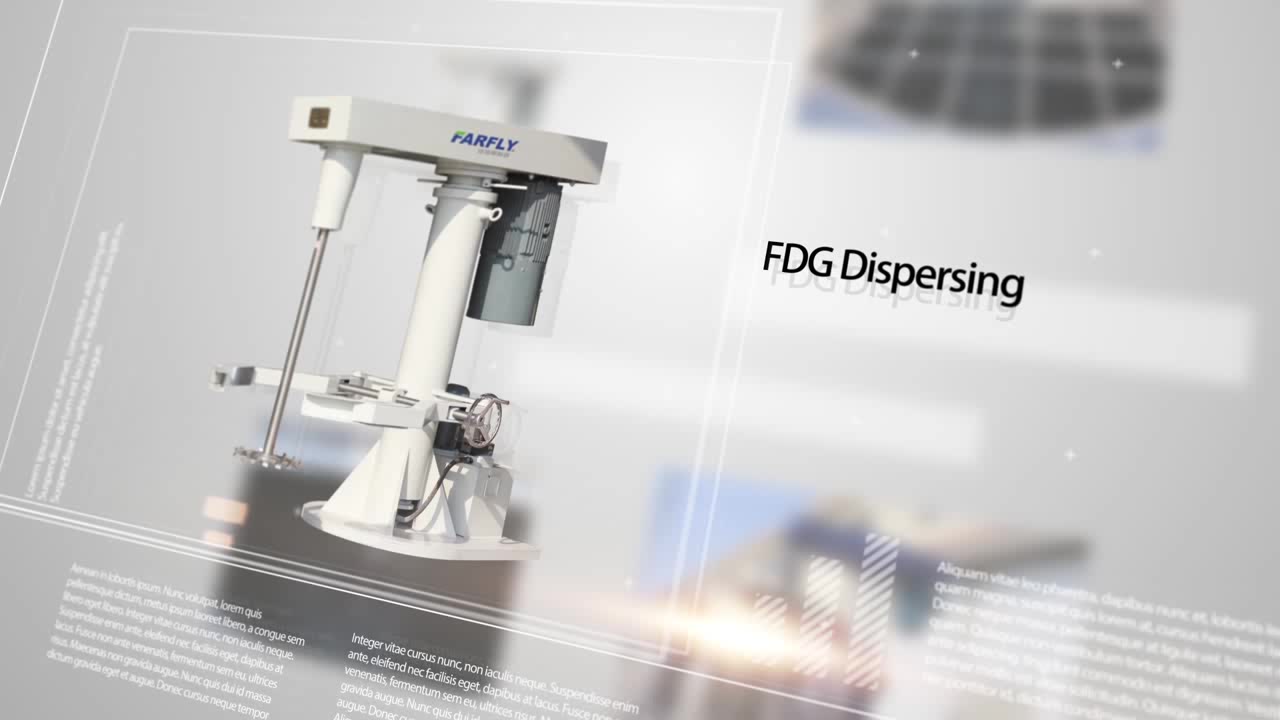
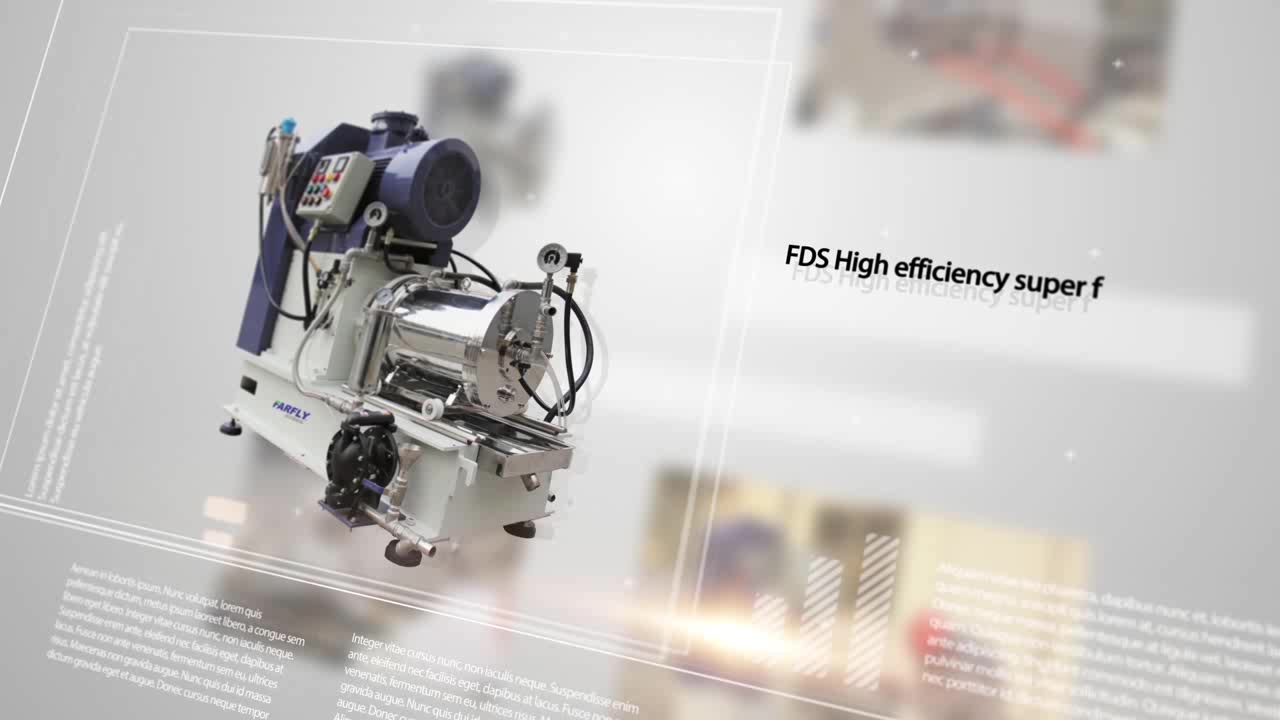
